Phenolic resin price April 2024 and outlook (see chart below)
- North America:US$1.79/KG, unchanged
- Europe:US$2.23/KG, -0.4% down
- Northeast Asia:US$2.17/KG, -0.9% down
- Africa:US$1.55/KG, unchanged
- South America:US$1.54/KG, -0.6% down
- India:US$2.13/KG, -0.5% down
Business Analytiq assumes no responsibility or liability for any errors or omissions in the content of this site. The information contained in this site is provided on an “as is” basis with no guarantees of completeness, accuracy, usefulness, fitness for purpose or timeliness.
Phenolic resin price index
This post is a summary of the global Phenolic resin price developments. The price developments of global Phenolic resin are expressed in US$ prices converted FX rates applicable at the time when the price was valid. Phenolic resin price index developments are calculated from multiple separate sources of data to ensure statistical accuracy.
The outlook for global Phenolic resin prices, on the second tab, is generated from different inputs including:
- Very recent price developments of immediate cost drivers of global Phenolic resin prices
- Recent price developments of underlying feedstocks which drive the price of Phenolic resin
- Market futures for both cost drives and feedstocks of global Phenolic resin prices
- Adjustment of current supply/demand imbalances in the Phenolic resin market
- Longer term trends in likely demand conditions
Further information on the Phenol resin price chart
What is Phenolic resin
Phenolic resin, also known as phenol-formaldehyde resin, is a type of thermosetting polymer that is widely used in various industrial applications. It is created through the polymerization of phenol (a type of aromatic compound) and formaldehyde (a simple organic compound). Phenolic resins are known for their excellent heat resistance, mechanical strength, electrical insulation properties, and chemical resistance. Here are some key characteristics and uses of phenolic resin:
Chemical Structure: Phenolic resins have a three-dimensional cross-linked structure formed by the reaction between phenol and formaldehyde. This structure results in the formation of methylene bridges (-CH2-) between the phenolic molecules.
Properties of phenolic resin
Heat Resistance
Phenolic resins exhibit outstanding heat resistance and can withstand high temperatures without softening or melting. This property makes them suitable for use in applications where exposure to heat is a concern.
Mechanical Strength
They have good mechanical properties, including high strength and stiffness, which make them valuable in applications requiring structural integrity.
Electrical Insulation
Phenolic resins are excellent electrical insulators, making them suitable for electrical components and insulating materials.
Chemical Resistance
They are resistant to many chemicals, acids, and bases, which enhances their durability and applicability in harsh environments.
Low Smoke and Flame Retardance
Phenolic resins have inherent flame-retardant properties and produce relatively low smoke when exposed to fire, making them valuable in fire-resistant applications.
How is Phenolic resin produced
The production of phenolic resin involves a chemical process known as the phenol-formaldehyde condensation reaction. This reaction polymerizes phenol and formaldehyde to create the three-dimensional, cross-linked structure characteristic of phenolic resins. Here are the basic steps involved in the production of phenolic resin:
Gathering Raw Materials
The primary raw materials for phenolic resin production are phenol and formaldehyde. Phenol can be derived from various sources, including petrochemicals or plant-based materials like coal tar or wood. Formaldehyde is typically produced by the oxidation of methanol.
Preparation of Phenol and Formaldehyde
The raw phenol and formaldehyde materials are prepared and purified to ensure they meet the required quality standards for resin production.
Mixing Phenol and Formaldehyde
In a controlled environment, phenol and formaldehyde are mixed together in the desired stoichiometric ratio. This mixture is often called the “resol” mixture.
Catalysis and Condensation Reaction
A catalyst, such as an acid or base, is added to the resol mixture. The choice of catalyst can influence the resin’s properties and curing time. The mixture is then heated, which initiates the phenol-formaldehyde condensation reaction. During this reaction, formaldehyde molecules react with phenol molecules to form methylene bridges (-CH2-) between the phenolic molecules. This cross-linking creates a three-dimensional network structure.
Control of Reaction Conditions
The reaction temperature, pressure, and duration are carefully controlled to achieve the desired degree of polymerization and resin properties. The reaction may be carried out in a batch or continuous process, depending on the production scale and equipment used.
Cooling and Solidification
After the desired degree of polymerization is achieved, the resin mixture is cooled to stop the reaction and solidify the resin.
Post-Treatment and Formulation:
The resulting phenolic resin may undergo additional processing steps, such as filtration and purification, to remove impurities and unreacted materials. Formulations may be adjusted by adding additives or modifying the resin to achieve specific properties, such as color, viscosity, or flame resistance.
What drives the cost of Phenolic resin
The cost of phenolic resin is influenced by several factors, and understanding these factors can help explain why the price of phenolic resin can vary. Some of the key drivers of the cost of phenolic resin include:
Raw Material Costs
The primary raw materials for phenolic resin production are phenol and formaldehyde. The prices of these raw materials can fluctuate based on factors such as supply and demand, production costs, and market conditions. Phenol can be derived from various sources, including petrochemicals or plant-based materials, and the choice of source can impact costs. Formaldehyde is typically produced by the oxidation of methanol, and its cost can also vary with methanol prices.
Production Scale
Economies of scale play a significant role in the cost of production. Larger manufacturing facilities can produce phenolic resin in larger quantities, which can lead to lower production costs per unit. Smaller or less efficient facilities may have higher production costs, affecting the final product’s price.
Energy Costs
The production of phenolic resin requires energy for heating, cooling, and other processes. Fluctuations in energy prices can impact production costs and, subsequently, the cost of phenolic resin.
Labor Costs
Labor costs, including wages and benefits for workers involved in the production process, can influence the overall cost of phenolic resin. Labor costs may vary depending on the location of the manufacturing facility and labor market conditions.
Transportation and Logistics
The cost of transporting raw materials to the manufacturing facility and shipping the finished phenolic resin products to customers can contribute to the overall cost. Transportation costs can vary depending on factors like distance, mode of transport, and fuel prices.
Quality and Additives
The use of additives or quality-enhancing measures can impact the cost. High-quality phenolic resins may require additional processing steps or the use of specific additives to meet certain performance standards, which can affect costs.
Regulatory Compliance
Compliance with environmental and safety regulations can add costs to the production process. Manufacturers may need to invest in pollution control equipment, safety measures, and waste management, which can influence the final product’s cost.
Research and Development
Investment in research and development to improve the properties of phenolic resin or develop new applications can contribute to costs. However, such investments can also result in higher-quality products that command premium prices.
Exchange Rates
For manufacturers that rely on imported raw materials or export their products, fluctuations in exchange rates can affect costs. Exchange rate movements can impact the cost of imported raw materials or the competitiveness of exported products.
Customization and Specialized Formulations
If customers require customized formulations or specialized properties in phenolic resin products, additional research and development efforts may be necessary, potentially increasing production costs.
Overall, the cost of phenolic resin is influenced by a complex interplay of these factors, and it can vary over time and from one manufacturer to another. Manufacturers carefully manage these factors to optimize production efficiency and maintain competitiveness in the market
What is Phenolic resin used for
Laminates
Phenolic resins are commonly used as binders in the production of laminated materials, such as phenolic laminates or phenolic sheets. These materials find use in electrical insulators, printed circuit boards, and decorative laminates for countertops.
Molding Compounds
Phenolic resins are used in the manufacture of molded components, including automotive parts, electrical connectors, and appliance handles.
Abrasives
They are employed in abrasive products, such as grinding wheels and brake linings, due to their hardness and heat resistance.
Coatings
Phenolic resins can be used in coatings and paints, providing durability and chemical resistance.
Adhesives
They are used in adhesive formulations, particularly in applications where high-temperature resistance and chemical resistance are required.
Foundry Binders
Phenolic resins are used as binders for molding and core sands in metal casting foundries.
Construction Materials
In construction, they are used in the production of phenolic foam insulation boards for thermal insulation purposes.
What types of phenolic resin are there
Phenolic resins can be categorized into different types based on variations in their chemical compositions, properties, and intended applications. Here are some common types of phenolic resins:
Novolac Phenolic Resins
Novolac phenolic resins are produced by using an excess of phenol compared to formaldehyde during the condensation reaction. They have a relatively low degree of polymerization and are more thermoplastic in nature. Novolac resins are often used as binders for molding compounds and in applications requiring good dimensional stability.
Resol Phenolic Resins
Resol phenolic resins are produced using an excess of formaldehyde compared to phenol during the condensation reaction. They have a higher degree of polymerization and cross-linking, making them highly heat-resistant and rigid.
Resol resins are commonly used in applications where heat resistance and mechanical strength are critical, such as in laminates, coatings, and adhesives.
Ortho-, Meta-, and Para-Substituted Phenolic Resins
These types of phenolic resins differ in the substitution pattern of the phenolic ring:
Ortho-substituted: Substituents are attached to adjacent carbon atoms on the phenolic ring.
Meta-substituted: Substituents are attached to carbon atoms separated by one carbon atom on the phenolic ring.
Para-substituted: Substituents are attached to carbon atoms separated by two carbon atoms on the phenolic ring.
These variations in substitution can affect the resin’s properties and reactivity.
Cresol Phenolic Resins
Cresol phenolic resins are produced using cresols, which are methyl-substituted phenols, as a primary raw material. They offer a balance of properties between novolac and resol resins and are used in a variety of applications, including molding compounds and coatings.
Modified Phenolic Resins
Manufacturers can modify phenolic resins by introducing additives or altering the formulation to achieve specific properties or characteristics. Modified phenolic resins may include resins with improved flame resistance, reduced formaldehyde emissions (low-VOC resins), or enhanced adhesion properties.
Oil-Modified Phenolic Resins
These resins are created by incorporating natural or synthetic oils into the phenolic resin formulation. Oil-modified phenolic resins are used in applications requiring flexibility and impact resistance, such as in foundry binders and abrasive products.
Specialized Phenolic Resins
Depending on the application and industry requirements, specialized phenolic resins may be formulated with specific attributes, such as electrical conductivity, UV resistance, or rapid cure times.
Bakelite
Bakelite is one of the earliest commercial phenolic resins developed by Leo Baekeland in the early 20th century. It is a thermosetting phenolic resin known for its electrical insulating properties and early use in various products, including electrical switches, kitchenware, and automotive components.
The choice of phenolic resin type depends on the desired properties and intended applications. Manufacturers often tailor the resin formulation to meet specific industrial needs, resulting in a wide range of phenolic resin variations available in the market.
Business Analytiq
BE THE FIRST TO SEE RISK AND OPPORTUNITY!
BusinessAnalytiq provides unlimited market trend data and an online tools to track market developments, key benchmarks & leading indicators.
BusinessAnalytiq leads to price visibility, better negotiations, easier budgeting and forecasting, lower raw material prices, and improved better internal and external communication. BusinessAnalytiq will decrease risk and higher profit.
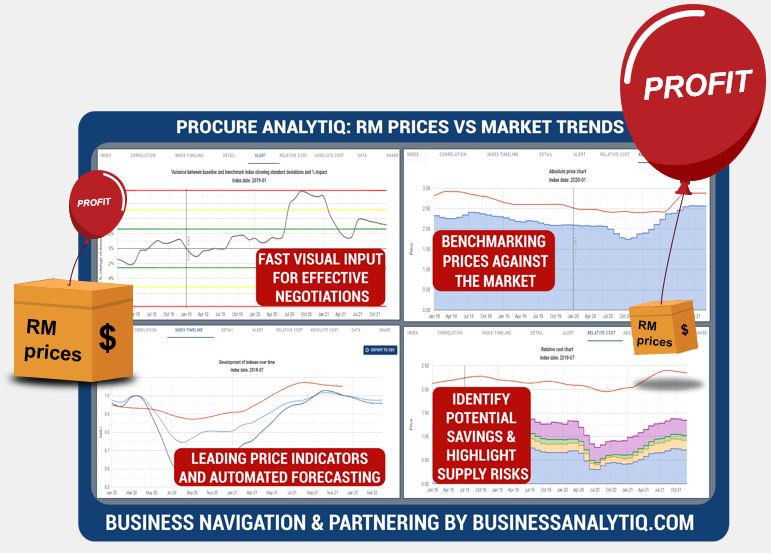
Where does the data come from?
- The source of the data are exclusively public non-confidential sources. We have no access to primary data
- This the index trend of the price trend of the "product category" in general, and not a single specification of the product in particular
- The data is a combination of contract and spot pricing
- Our algorithms are set up to eliminate significant product mix impact on the reported price
- We combine public publications, import/export records, trading prices, company announcements, magazine articles, tweets, and other sources of ad-hoc public information.
- The chart shows the our best approximation of the market trend based on our algorithm interpretation of the signals
- For most indexes we have multiple sources and we focus on using statistically-correlated sources
- As a function of our automation, it is likely that recent trends will be adjusted as we discover more information. So, for example, the price trend for February 2024 will be first calculated in February 2024 and adjusted in March, April and May 2024.
- We will update the data trend as more information becomes available, and this means that recent trends will always be adjusted as we get more data available
- The algorithm will regularly revise our understanding of market trends, and indicated market trends may change
- The data is presented in US$. The UOM of measure is shown in the Index list table
- Our automated software and we do our best to create an accurate representation of the trend
Where does the data NOT come from?
- We do not purchase data from any other source and republish it.
- We will not purchase data from any other source and republish it
- We do not extrapolate trends, even for the forecast. We look for other market signals and leading indicators
What data should our company use?
- If you are making decisions driving significant share of profit, we always recommend that you buy data from the companies who invest in direct primary market access such as ICIS, amongst many others
- Our data, at best, represents an estimate of the market trend based on public information
- We have no direct access to the market, and we do not interview suppliers and customers
- Our automated analysis tools in the online software are set up to combine our data with other sources of data
- We do not recommend that you use our data for direct price mechanisms, as we may change and improve the data trends over time, including historical data
What does the quality indication in the main menu mean?
- Quality level A: Data is from a reliable and confirmed source
- Quality level B: Data is from multiple credible sources and there are no major statistical inconsistencies between them
- Quality level C: Data is from multiple credible sources and there are some statistical inconsistencies between them
- Quality level D: Data is from a single credible source, but we cannot verify the data
- Quality level E: Data is either:
- From a single source, which we consider reliable, but we cannot verify the data.
- From 2 or more sources which have some periods of contradicting trends.
- Quality level F: Data is from a single source which we consider indicatively correct, but the data is anecdotal and we cannot verify the data.
What are the disclaimers?
- We assume no responsibility or liability for any errors or omissions in the content of this site.
- The information is provided on an “as is” basis with no guarantee of completeness, accuracy, usefulness, fitness for purpose or timeliness.
- By their nature, outlooks are always uncertain
How often do we update the data?
- We aim to update the data series on the 9th and 24th of each month (but we do not always make it for each chart)
- The data for the current month and recent history are fine-tuned over time.
What are we doing to improve the data?
- We are continually improving our data collection and processing methods
- Pricing data will be updated from time to time as we improve the accuracy
- We are reviewing all data sources in the first half of 2024.
- There will be continuous fine-tuning of the trend and forecast algorithm as part of that.
- The key focus in 2024 is to add many additional indexes
How can i give feedback on the data or request for new indexes
- Feel free to contact us if you have a specific request. You can reach us via the Contact us page